Thermal Management Materials for the Future
In this competitive Thermal Gap Fillers market, we provided the best professional solution plans for our customers. To respond to the rapid growth in technology, our team thrives to create thermal products that reduce our products environmental impact and improve trading arrangements for key technologies. To maintain our competitive advantage, we increase our intellectual property, encourage innovation, and seek to develop innovative patents for new thermal products.
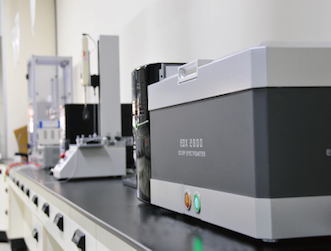
Thermal Gap Fillers, GAP PAD Keeping up with the advancements in technology is challenging. Our thermal engineers push the boundaries of technology to develop the most advanced thermal products on the market. Our thermal engineers are committed to developing innovative solutions to address the challenges facing system designers around the globe. Our research and development team works closely with our customers to develop products to fit their specific requirements.
Product Categories
Thermal gap fillers are essential components in the thermal management of electronic devices. These pads are designed to fill the gaps between heat-generating components and heat sinks or other cooling mechanisms, ensuring efficient heat transfer and protecting the devices from overheating. There are two primary categories of thermal gap filler pads: silicone-based and non-silicone-based, each offering distinct advantages depending on the application.
Silicone-Based Thermal Gap Filler Pads
Silicone-based thermal gap fillers are widely used due to their excellent thermal conductivity and flexibility. These pads are soft and conformable, allowing them to fill even the smallest and most irregular gaps between components. This ensures that there is optimal contact between surfaces, which is crucial for effective heat dissipation.
Silicone pads are also known for their durability and ability to withstand high temperatures and thermal cycling. They maintain their performance over a wide range of temperatures, making them ideal for applications in automotive electronics, telecommunications equipment, and consumer electronics. Additionally, silicone-based pads provide good electrical insulation, which helps protect sensitive components from electrical shorts and other damage.
Non-Silicone Thermal Gap Filler Pads
Non-silicone thermal gap fillers are designed for applications where silicone contamination is a concern, such as in optical devices, cleanroom environments, or sensitive electronic components where outgassing must be minimized. These pads offer similar thermal conductivity and conformability to silicone pads but are made from alternative materials that eliminate the risks associated with silicone.
Non-silicone pads are also highly effective in providing thermal management in devices that require low outgassing and where purity is critical. These pads are often used in industries such as aerospace, medical devices, and precision electronics, where maintaining the integrity of the surrounding environment is crucial.
Choosing the Right Thermal Gap Filler Pad
When selecting a thermal gap fillers, it’s essential to consider the specific requirements of your application. Silicone-based pads are generally the preferred choice for most applications due to their thermal performance, flexibility, and durability. However, in specialized environments where silicone contamination or outgassing is a concern, non-silicone pads offer a safe and effective alternative.
Both silicone and non-silicone thermal gap filler pads are crucial for ensuring the performance and reliability of electronic devices. As electronic components continue to evolve and become more compact, the need for effective thermal management solutions like these pads will continue to grow.
In conclusion, whether you choose silicone-based or non-silicone-based thermal gap filler pads, both options provide robust solutions for managing heat in electronic devices. Selecting the right type of pad can significantly enhance the performance and longevity of your equipment, making it a critical decision in the design and maintenance of electronic systems.
LiPOLY TIM Technology : Thermal Solutions
Do you have some questions? Please don’t hesitate to send us an email: [email protected]